What are the prospects for Georgia’s furniture sector?
There is a gap in Georgia’s normally vibrant arts and crafts scene: furniture. Excellent news for furniture importers, who see their current sales rises continuing. But sad for Georgian culture, as few artists or crafts people are making the Georgian antiques and heirlooms of the future, though there are some stunning successes.
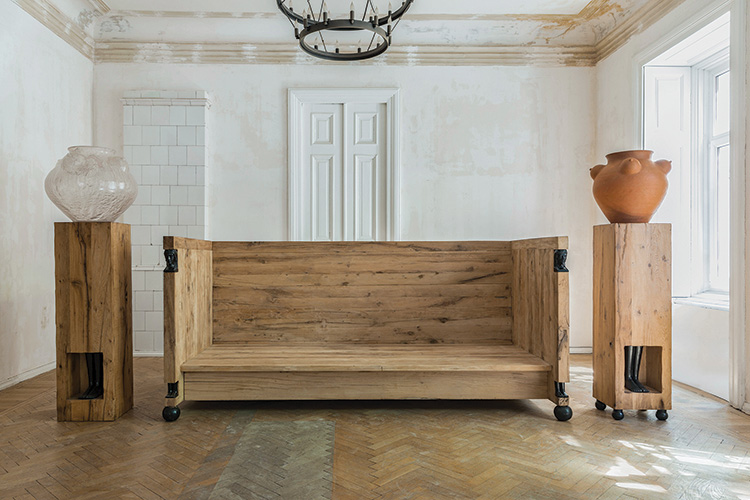
The most notable of these are the collections by Nata Janberidze and Keti Toloraia at Rooms Studio, who also consult for Adjara Group’s hotels, including on ambitious projects such as the interiors of Rooms Tbilisi, Kazbegi, and Kokhta (they designed the latter two). Their evocative, sculptural works have featured in just about every design magazine internationally, helping raise Georgia’s cultural profile.
Demand for high-quality Georgian furniture is certainly not lacking either at home or abroad. Rooms Studios’ medieval styles have featured on gallery websites and at art fairs around the world and sell at undisclosed (but undoubtedly high) prices in the U.S. and Europe. The contemporary fashion for fitted furniture is also being catered to by Georgian production and exported to Europe and the U.S. by several producers.
For some years now donor supporters have been active, doing their best to grow local furniture production in volume and breadth into a healthy industry. But the fact remains, as detailed in a report for USAID by the Washington-based Policy and Management Consulting Group (PMCG) and Georgia’s International School of Economics at Tbilisi State University’s Policy Institute (ISET), this is not working. It states: “even though there is some potential for upgrading the value chain, it does not show a significant capacity for significant expansion.”

Furniture production remains less than 2% of the economy, according to the latest report for Enterprise Georgia commissioned by the Commission of Foreign Affairs of Lithuania. The reasons for the absence in scale, particularly at the top end of the market, and the scarcity of collectible items, are a bit daunting.
According to the industry analysis for USAID, just about all the essentials for a creative furniture industry are missing in Georgia. That ranges from reliable sources of local high quality seasoned hardwoods, easy access to finance, skilled workers (who have migrated to higher wage countries), and especially, the vital creatives: interested artisans and artists themselves.

Maybe it is also the fault of the domination in the arts historically in Georgia of textiles, painting, and metalwork. Furniture hardly features, the most valued traditional feature of Georgian wooden household objects for seating or sleeping are the carvings.
“These challenges persist in the value chain, and no significant steps have been taken to address them,” commented the USAID report, in its look at 2022’s state of furniture production and its value chain. It put the import figure for furniture and furniture components in the first half of last year at nearly GEL 50 million, a rise of around a third. Turnover as a whole (mostly imports) in the value chain in that period put it at GEL 65 million, a rise of 21% compared to a year earlier.

Furnishing components seem a more vibrant business. Companies named in the reports on manufacture of semi-finished products include Madera Georgia and CRP Wood, who produce paneling. The USAID analysts also found that services and equipment producers were growing in number. Another success, although in an unusual area of this sector, is Georgian Producers, which makes pet furniture and has been exporting to the UK and EU.
Geostat statistics show that local furniture production has been increasing in recent years, with output growing from GEL 50 million in 2010 to GEL 203 million in 2018, according to comments in the EU report on a project seeking to build a Georgian furniture cluster. Then, “negative dynamics” arrested growth, including soaring wood prices, Covid’s hit on the economy, and Georgians’ falling spending power. Last year, efforts to build a cluster stopped.
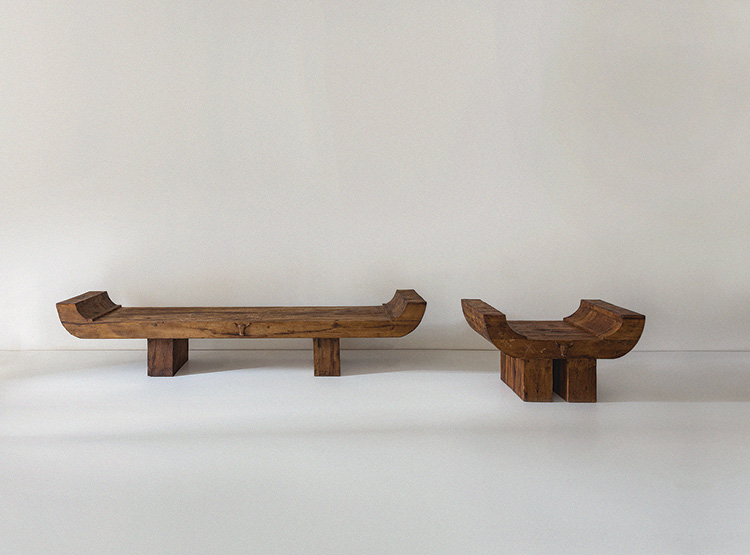
Yet production continues to expand at some levels and installation of fitted furniture and components, at least, are growing, even if constructed with imported MDF or laminates. Since so much of the work is done by individual craftsmen or unregistered businesses, the numbers, says EU research, are hard to track accurately. Statistics from Geostat have been showing a growing level of employment (which is perhaps why it is so hard to find anyone who can fix a shelf or assemble a cabinet), no doubt due to work in the Tbilisi and Batumi apartment building boom, the new rural houses, and the increasing number of small hotels and guest houses.
Collective efforts
Wider analysis shows that Georgian artisans, encouraged by donors, have tried working in groups in order to boost the power of their marketing. One such is the Association Design Georgia, which has been operating since 2019. At the end of last year, it had 20 members, all among other things, working in furniture design – companies and individual craftspeople – and this is seeking to expand. What the association provides is help in participating in international exhibitions, and also it plans to open a donor-backed store.
Another group, the Georgian Woodworkers and Furniture Manufacturers Association, has been trying to help local manufacturers make high quality products so that they can export. However, this is extremely hard given the competition from the vast, well-established European furniture companies and cheap production from Asia. With low levels of cooperation within the Georgia furniture sector, “the government, companies and stakeholder initiatives are often too scattered and fail to induce significant progress,” comments the USAID report.
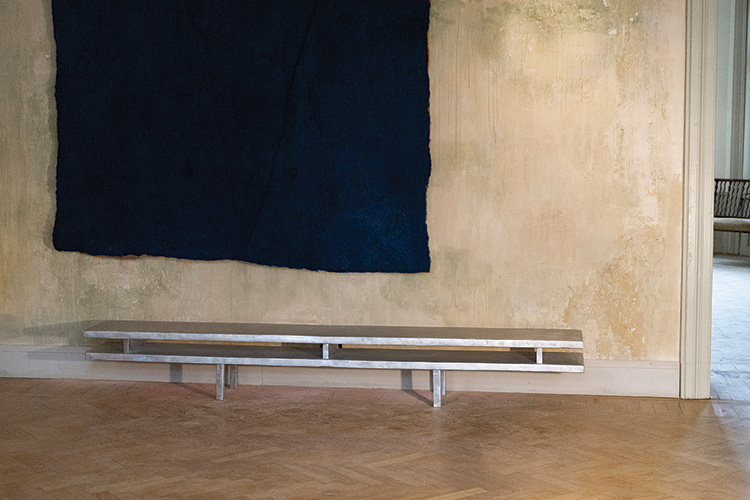
At the moment, Georgian furniture makers cannot seem to use any of the advantages given by DCFTA. One problem the report compiled for the EU mentions is that most producers are SMEs and are ill-equipped for international marketing and for meeting international regulations. Difficulty in raising small producer’s games in product terms can be another problem, it says, as SMEs can be reluctant or cannot afford to work with designers. Yet, all commentators agree on solutions and government actions that would help local production, and not only in the niche, upmarket, and high end of the furniture sector.
For a start, according to the EU report, there is a huge need to train more skilled workers, then to ensure that there is affordable finance for SME producers and that high-quality hardwood is more easily obtainable. The latter is problematic because illegal logging can make domestic supply unstable, says the USAID report.
Substantial investment is needed to replace imported materials, the EU report states, although it sees the widespread availability of beechwood as offering good potential. The production of veneered beechwood panels it considers as having “good potential” for Georgia, and “potentially generating vast employment opportunities in the country,” aiming for both local consumption and for export.
Further development in online sales development is another USAID report recommendation, having found that one company, LTD Conibe, is selling around 90% of its production this way.
Yet the crux of success, and a millennium-old challenge for artists and craftspeople, is to find a strong stake-holder or backer. As the USAID report comments, the Georgian furniture value chain “lacks strong stakeholders with the will and resources to undertake needed actions.”
Rooms Studio
These factors have been major elements in the success of Rooms Studios – their strong and long relations with the Adjara Group, and a steady stream of commissions. Plus, the Rooms Studios duo have a great sense of theater, which is of enormous help in marketing.
Rooms Studios founders, who started their business in 2007, having met at art school where they studied interior design, are designing for the top international market bracket, their handmade sculptural objects produced as limited or numbered editions and made to order. At this level, and with the benefit of prestige prices, they are able to say that “we have been exceptionally fortunate to discover and collaborate with incredible local craftspeople, many of whom have contributed to our work for over a decade.”
Their pieces call heavily on what Nata Janberidze and Keti Toloraia refer to as combining their “native Georgian heritage with a contemporary aesthetic,” working with large-scale sculptural forms and mixed-media textural materials. Looking at the pieces, it is easy to imagine that they could have been made 300 years ago or more for a medieval Georgian fortress.
“It fills us with great pride to know we have a small role in preserving the traditional local hand-carving techniques that have become an inseparable part of our collections,” they say. The “skilled wood handcrafting techniques of our ancestors” have become an integral part of their collections.
This is not the only way they are contributing to Georgia’s arts culture as they are also doing something advocated by the EU reports for growth in the Georgian furniture sector, which is establishing collaborations with other artists. They invite others – ranging from photographers to graffiti artists – to create works for their collections, thus building a strong gallery and exhibition presence for Georgian work. The international design world is always agog to see what they will present next.
Given the range of working examples, and the potential sales domestically from import-substitution alone, donors remain optimistic that the Georgian furniture sector can grow. And it appears understandable that Enterprise Georgia has named the Georgian furniture sector as “one of the most attractive for investors.”